サニースタッフブログ
信頼と安心を裏側で支える「生産管理課」のご紹介
2024-02-06
今回は、弊社の「生産管理課」に関する記事をお届けします。事業で必要な材料の購買から、商品の供給までをスムーズに行えるように日々業務に励んでいる当社の生産管理課。同課で働くTさんに、材料購入・受け入れ、在庫管理等の業務の中で留意していることをお聞きしました。
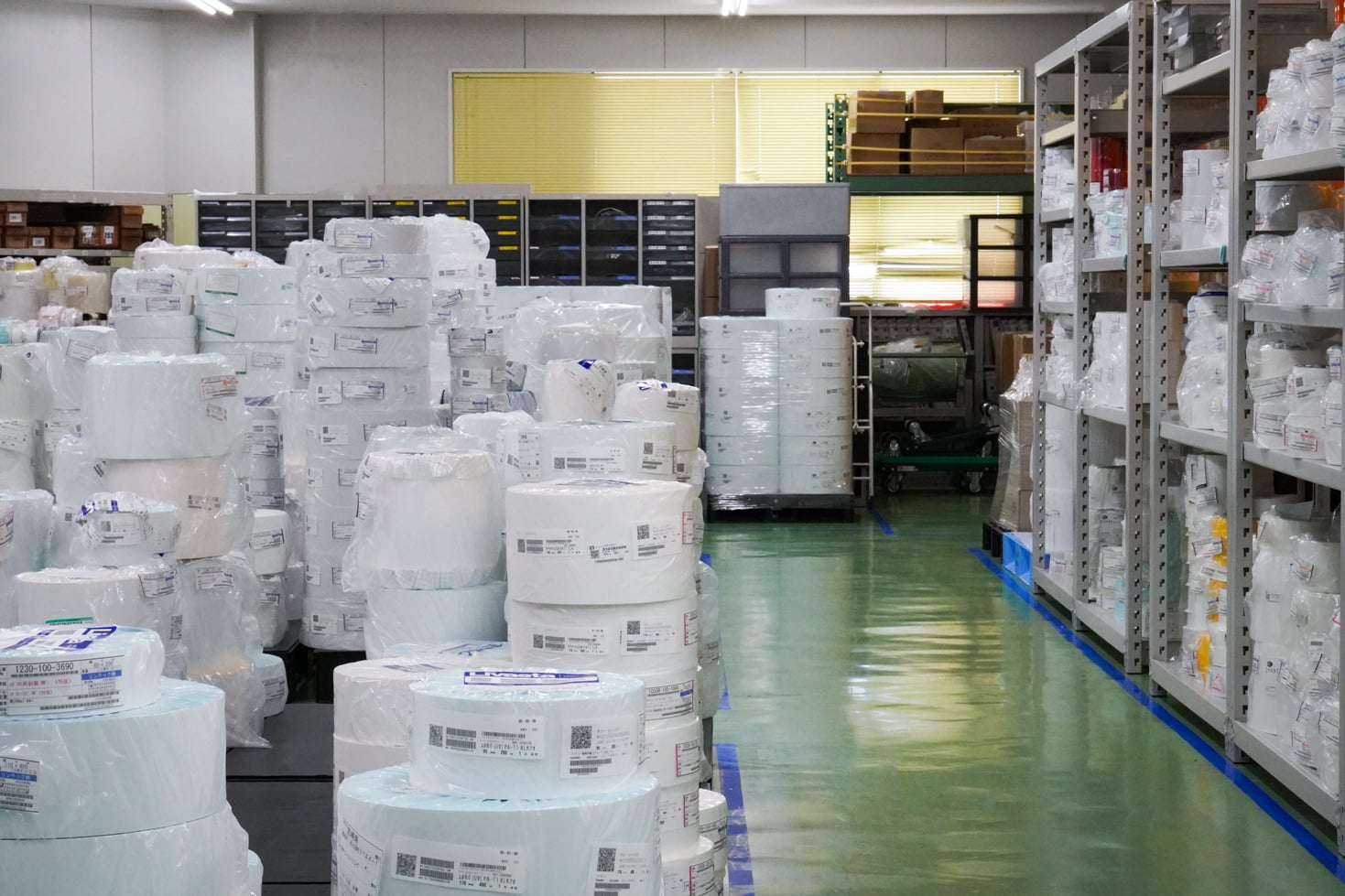
――― 材料を発注するときに留意していることはありますか。
Tさん:私が材料発注する際は、『無駄なく必要な分だけを購入できるように、効率よく注文すること』を意識しています。
シール・ラベル印刷の場合、ラベルのデザインが一部変わるだけで、形状、サイズ、材質も全く同じものを同時につくる場合があります。例えば特定の商品のシリーズものなど、タイトルや柄の一部だけが異なるような類似品ですね。そのような類似品を印刷する場合は、抜き型(刃型)をラベルの種類ごとに変える必要がないため、刃型をセットする際の調整用の(予備)材料も一回分で済みます。つまり、3種類の印刷を同時に行えば、その調整材料は1/3で足りるわけですね。そこで、類似品の印刷がある際には、そこを考慮して発注の量を調整するようにしています。
――― 製造に必要な分だけを頼むということは、「その製品の作り方(製造方法)」も把握しているということでしょうか。
Tさん:はい、そうですね。私自身は、元々生産管理課に配属される前、シール・ラベル印刷に必要な版下(印刷用)データを作成する部署にいました。ですので、直感的に「この製品の時はこうやって印刷されるな」というのが分かるんです(笑)。
また、シールの材料(原紙)は、原紙メーカーさんの方で大きなロール状の原反から当社が希望する材料を切り出してもらい、その原反1本分を一括購入することもあります。その際は、注文頻度の多い製品の幅を確認して、できるだけ端数(端材)が出ないように組み合わせて注文を行なったりもしています。
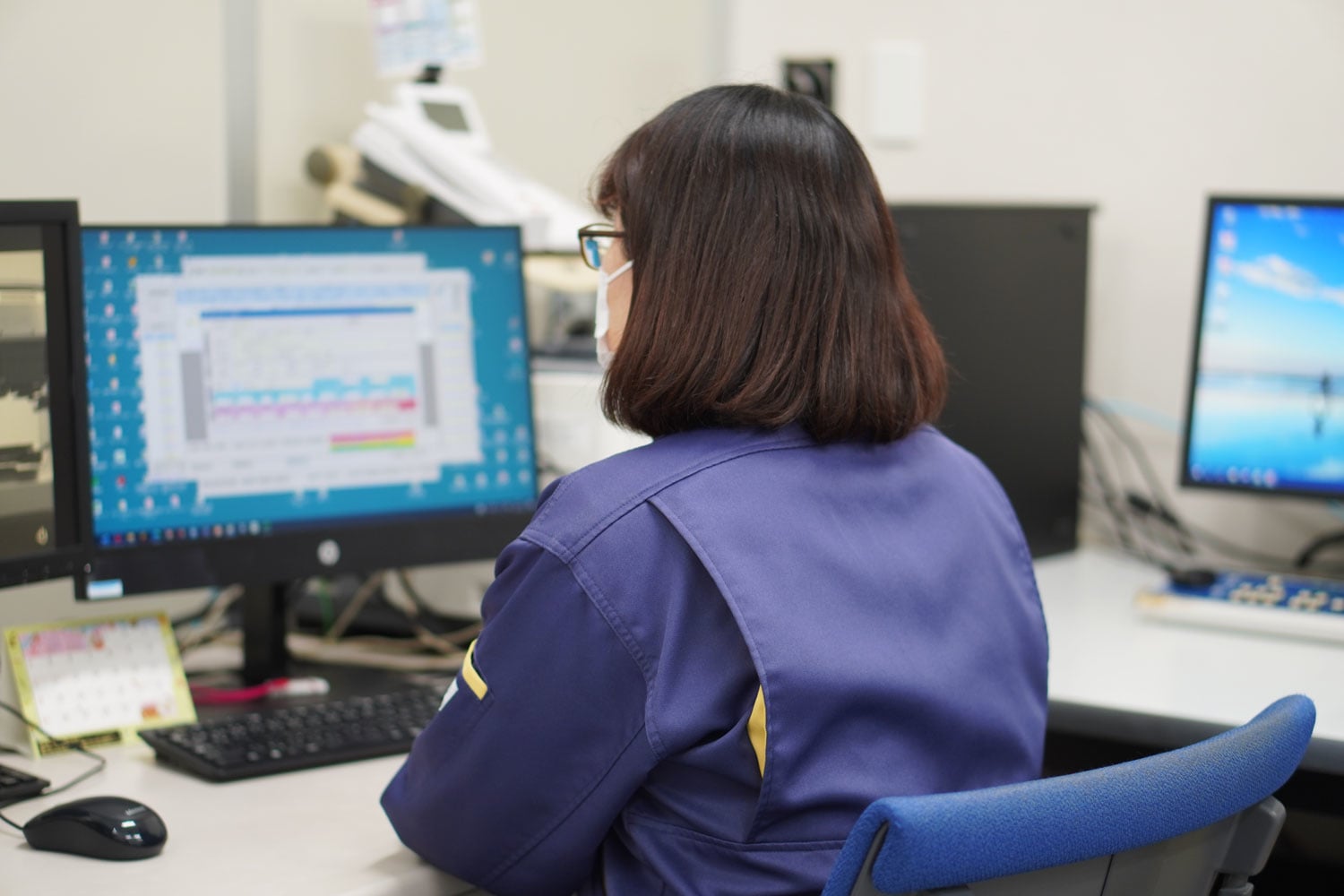
――― 購入した材料の受け入れ体制についてもお聞きしたいです。
Tさん:材料受入の際に在庫受入管理ラベルを貼るのですが、そこに記載されているQRコードと、購入した材料に貼られているQRコードを読み取ることで、発注した製品と届いた製品が異なっていないかを確認しています。仮に発注した材料と異なるものが入ってきたとして、誤って現場に届いてしまうと、大変なことになります。最悪、製造ラインを停めてしまうので、生産管理課としての受入作業は重要です。ですが、受入チェックシステムと、私たちの慎重な作業により、幸い、過去にそのようなミスは発生していません。
――― スムーズに確認作業が行えるような体制が整えられているのですね。在庫の管理についても教えてください。
Tさん:まず在庫の管理に関しては、「先入先出」を重視しています。注文が入った際は、社内の在庫を確認して、そこから優先的に材料を引き当てます。昔は、いざ材料を引き当てようとしたときに、どこに何があるのか把握できる仕組みが出来ておらず、非常に引当業務や棚卸業務が大変でした…。
――― 現在は改善されているということですね。どのような改善方法を取られたのでしょうか。
Tさん:現在は『棚番』という数字を材料ごとに振って、在庫の保管管理を行なっています。材料を保管している棚に住所のようなものが割り振られているのですが、この材料はこの住所にあるというのが紐づけられているため、材料を探す作業が一気に楽になりました。大きな業務改善だったと思っています。
Tさん:材料受入の際に在庫受入管理ラベルを貼るのですが、そこに記載されているQRコードと、購入した材料に貼られているQRコードを読み取ることで、発注した製品と届いた製品が異なっていないかを確認しています。仮に発注した材料と異なるものが入ってきたとして、誤って現場に届いてしまうと、大変なことになります。最悪、製造ラインを停めてしまうので、生産管理課としての受入作業は重要です。ですが、受入チェックシステムと、私たちの慎重な作業により、幸い、過去にそのようなミスは発生していません。
――― スムーズに確認作業が行えるような体制が整えられているのですね。在庫の管理についても教えてください。
Tさん:まず在庫の管理に関しては、「先入先出」を重視しています。注文が入った際は、社内の在庫を確認して、そこから優先的に材料を引き当てます。昔は、いざ材料を引き当てようとしたときに、どこに何があるのか把握できる仕組みが出来ておらず、非常に引当業務や棚卸業務が大変でした…。
――― 現在は改善されているということですね。どのような改善方法を取られたのでしょうか。
Tさん:現在は『棚番』という数字を材料ごとに振って、在庫の保管管理を行なっています。材料を保管している棚に住所のようなものが割り振られているのですが、この材料はこの住所にあるというのが紐づけられているため、材料を探す作業が一気に楽になりました。大きな業務改善だったと思っています。
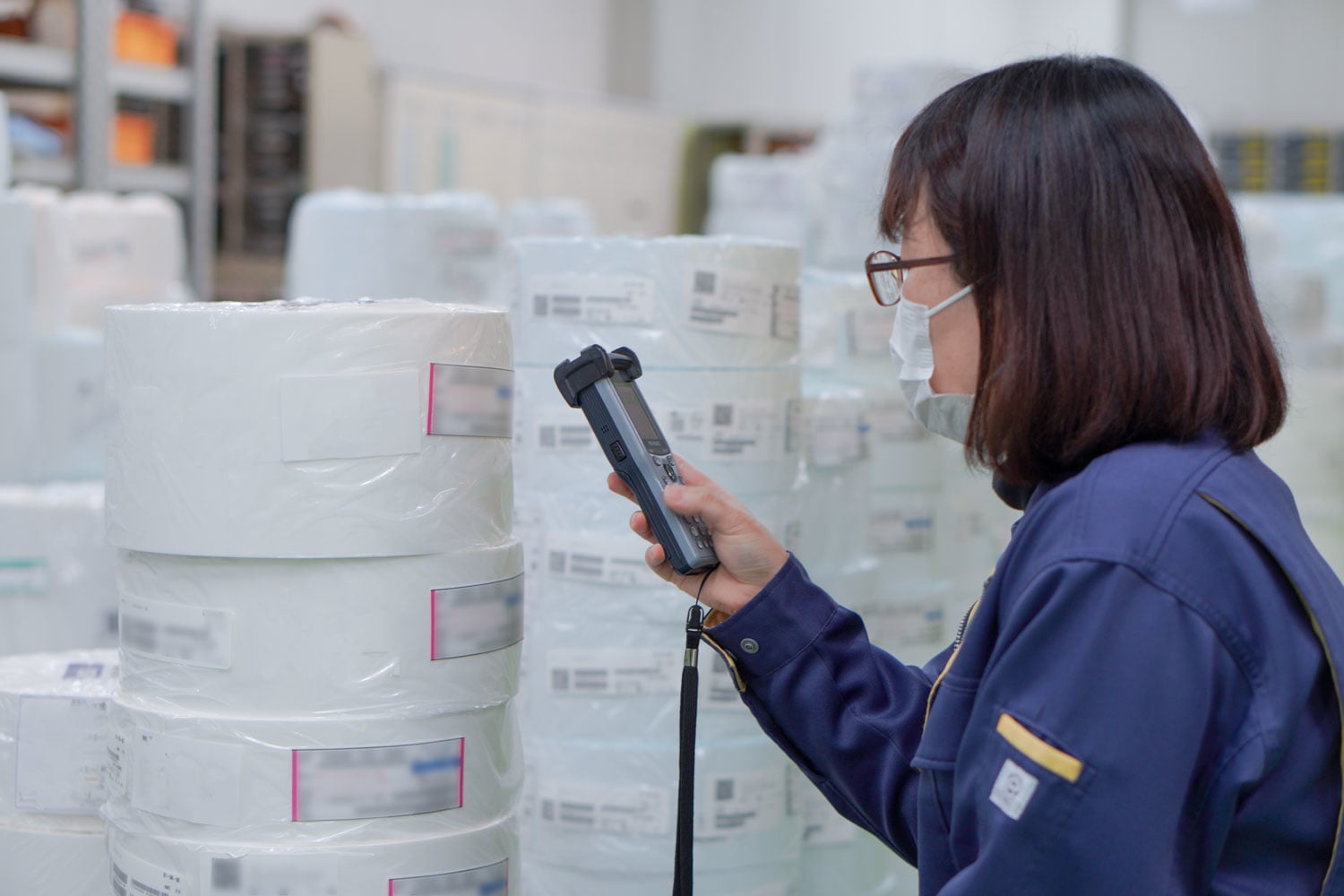
――― 材料の引当など、便利になったものもあると思いますが、当社で現在進んでいるDX化の観点から、このような改善をしていきたいというものはあるでしょうか。
Tさん:今考えているのは、RFIDを用いた材料の追跡です。この材料は今どこにあって、どのタイミングで在庫管理の部屋から出たのか。などをリアルタイムで追えるようになることで、より正確に、かつ容易に在庫の管理が出来るのではないかと思っています。
また、AI技術を用いて注文の傾向分析・予測。そこから発注を行う事が出来るようになれば、私が現在行っている経験や勘による予測を行う必要がなくなり、誰でも同じように無駄なく発注が出来るようになると思います。
――― 製品をお客様の元へスムーズに提供できているのは、生産管理課が縁の下の力持ちとなって、日々業務を行っているからだと改めて感じることが出来ました。
Tさん:今考えているのは、RFIDを用いた材料の追跡です。この材料は今どこにあって、どのタイミングで在庫管理の部屋から出たのか。などをリアルタイムで追えるようになることで、より正確に、かつ容易に在庫の管理が出来るのではないかと思っています。
また、AI技術を用いて注文の傾向分析・予測。そこから発注を行う事が出来るようになれば、私が現在行っている経験や勘による予測を行う必要がなくなり、誰でも同じように無駄なく発注が出来るようになると思います。
――― 製品をお客様の元へスムーズに提供できているのは、生産管理課が縁の下の力持ちとなって、日々業務を行っているからだと改めて感じることが出来ました。
DX化が進んでいくことで、今まで以上に便利に、そしてより効率的にお客様に製品を届けることが出来るようになっていくと思います。サニーシーリングでは、さらなる効率化と社内改善に取り組みむと同時に、お客様に喜んでいただけるような仕組みづくりを続けてまいります。
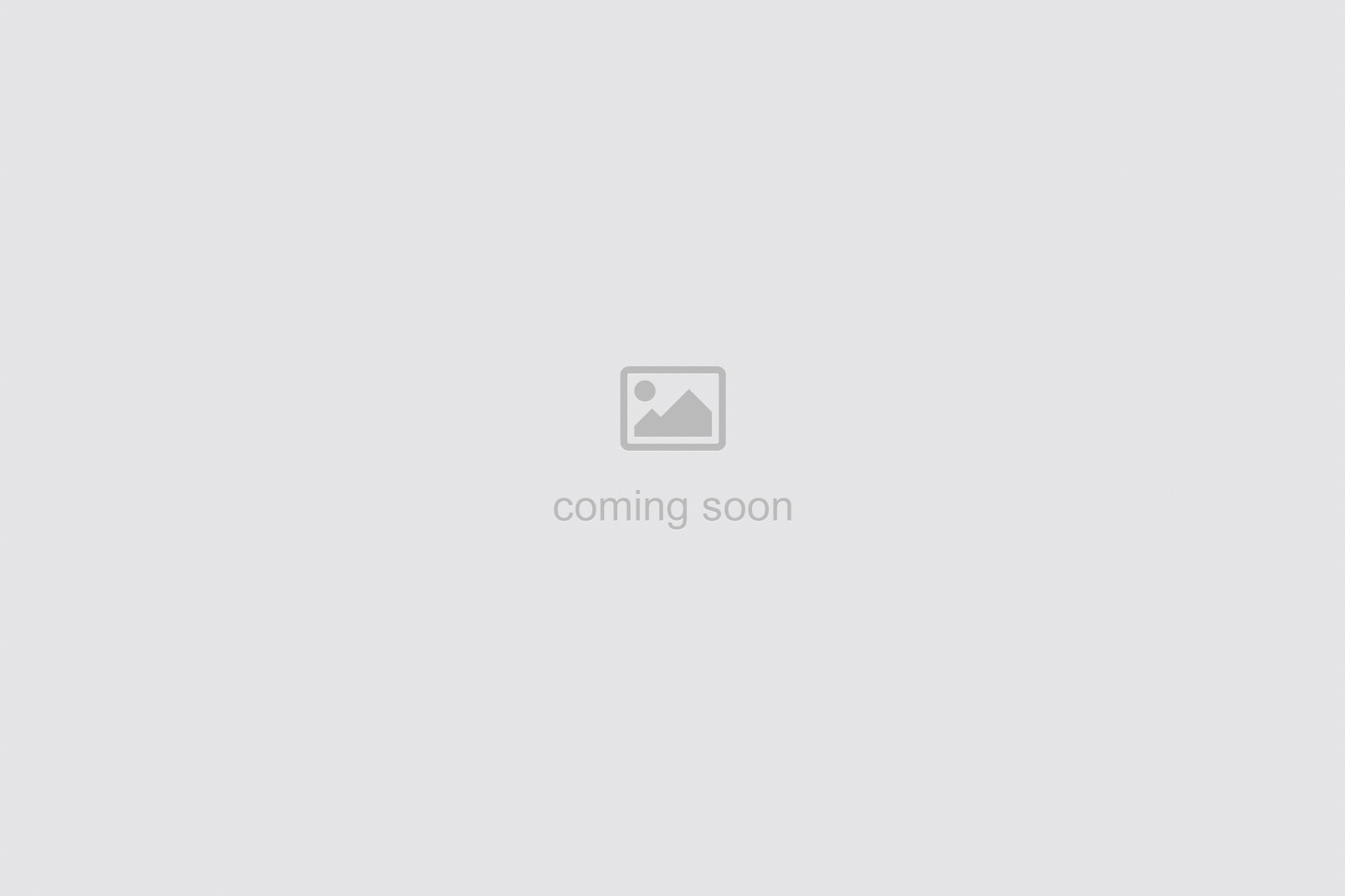